Plastic extrusion is a high-volume manufacturing process in which raw plastic material is melted and formed into a continuous profile.
Plastic extrusion is a high-volume manufacturing process in which raw plastic material, often in the form of pellets, is melted and formed into a continuous profile. This technique is commonly used to produce items such as piping, tubing, weather stripping, fencing, deck railings, window frames, and plastic films.
The process involves feeding the plastic material into a heated barrel, mixing it up, and forcing it through a die to shape it into a particular form. The plastic then cools and hardens, retaining its shape as it is cut to the desired length.
This article will delve into the specifics of plastic extrusion, including its various types, the materials used, its advantages, and its vast applications in construction.
Key takeaways
- Plastic extrusion is a high-volume manufacturing process for shaping plastic.
- It involves heating, shaping, cooling, and cutting the plastic.
- Types of extrusion include tubing, blow film, sheet film, and over jacket.
- Materials used include PVC, HDPE, PP, LDPE, and PS.
- Advantages include high-speed production, design flexibility, affordability, structural integrity, and sustainability.
Definition of Plastic Extrusion

Plastic extrusion is a high-volume manufacturing process wherein raw plastic material is melted then formed into a continuous profile. It is how plastic shapes such as pipes, seals, and plastic sheeting are made.
It involves several steps:
- Pre-drying: The plastic pellets are typically dried in a hopper before processing. This removes any moisture that could cause defects in the final product.
- Melting: The dried pellets are fed into an extruder. The extruder’s barrel has a large screw thread that turns, heating and pressurizing the plastic to a molten state.
- Shaping: Once melted, the plastic is forced through a die – a shaped hole – that gives it its final shape. The types of shapes created depend on the specific type of extrusion process used.
- Cooling: The extruded plastic is cooled, typically by air or water, so it retains its new shape.
- Cutting: After cooling, the plastic is cut to the desired length, finishing the extrusion process.
This represents the basic journey of plastic extrusion, from raw pellets to finished product. Each step along the way offers opportunities for manufacturers to create a wide variety of shapes and dimensions, catering to a multitude of different construction applications.
The Process of Plastic Extrusion
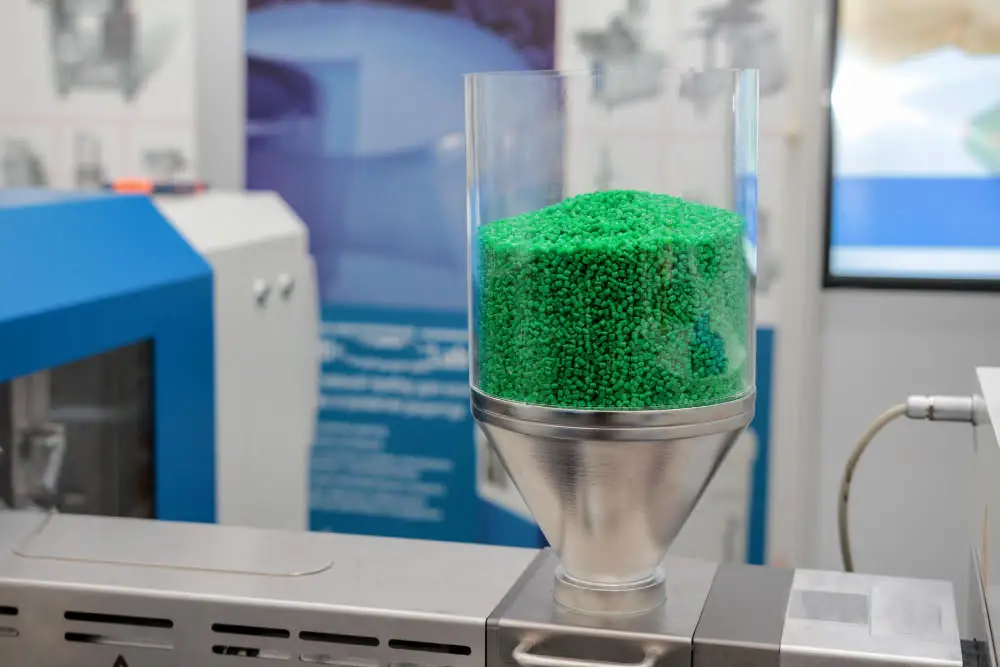
Extrusion begins with a collection of raw plastic materials, known as resins or pellets. These are fed into the inlet of an extruder, a machine driven by a motor. The extruder heats the plastic to its melting point and mechanically manipulates it. Meanwhile, the motor powers a rotating screw, which pushes the liquefied plastic through a shaping die.
As the heated plastic exits the die, it takes the die’s shape, forming a continuous profile. This profile is cooled, either by air or water, to solidify it. The final step involves cutting the profile into desired lengths or winding it onto a spool for later use.
Key to note–
- Type of plastic: Determines melting point and the necessary cooling method.
- Screw design: Impacts efficiency and quality of final product.
- Die design: Shapes the extrusion profile and affects the product’s final dimensions.
- Cooling process: Ensures the profile holds its shape and achieves desired properties.
- Cutting or reeling: Makes product ready for packaging or further processing.
Types of Plastic Extrusion: Tubing, Blow Film, Sheet Film, Over Jacket
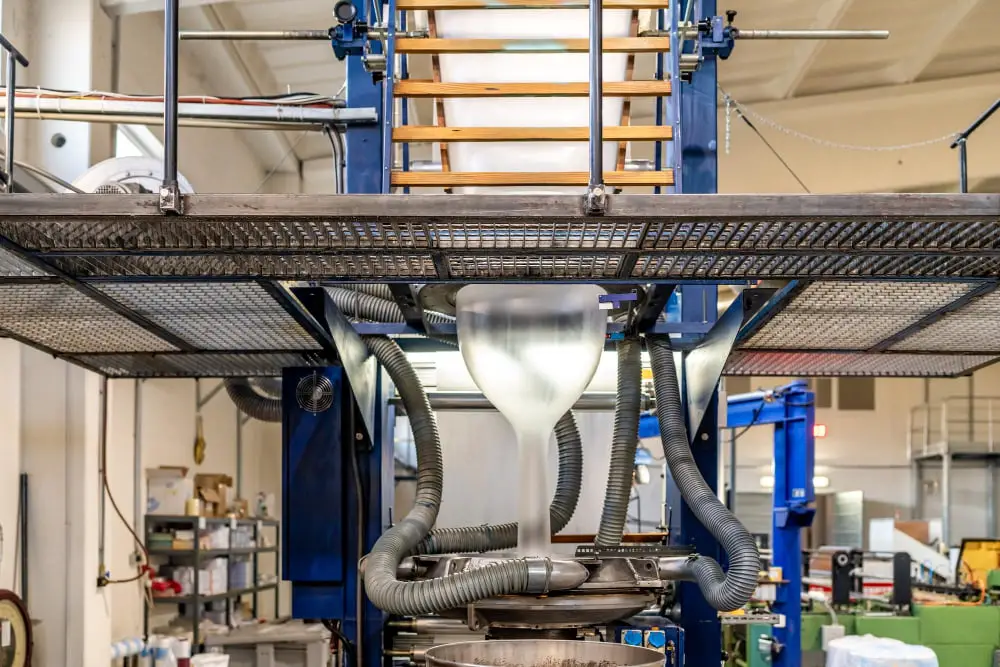
Tubing is the most common type of extrusion, widely used in the construction industry for plumbing purposes. This method involves forcing the molten plastic through a die, which shapes it into a tube.
Blow Film extrusion, on the other hand, is best suited for producing materials like shopping bags and packaging films. The process involves forming a tube by inflating the hot plastic and then cooling it down to create a thin, strong film.
Sheet Film extrusion is a method that creates larger flat plastic sheets. These sheets can be used in a variety of applications, from automotive components to greenhouse coverings.
Over Jacketing extrusion is used to create a secondary protective layer over an existing product, such as an electrical wire. This not only provides protection but adds additional properties to the product, like water resistance.
Regardless of the type of plastic extrusion, the process involves four key steps: plastic pellet selection, heating and melting, shaping through the die, and cooling. The plastic’s properties and the chosen method directly determine the final product’s quality, shape, and application.
Typical Materials Used in Plastic Extrusion
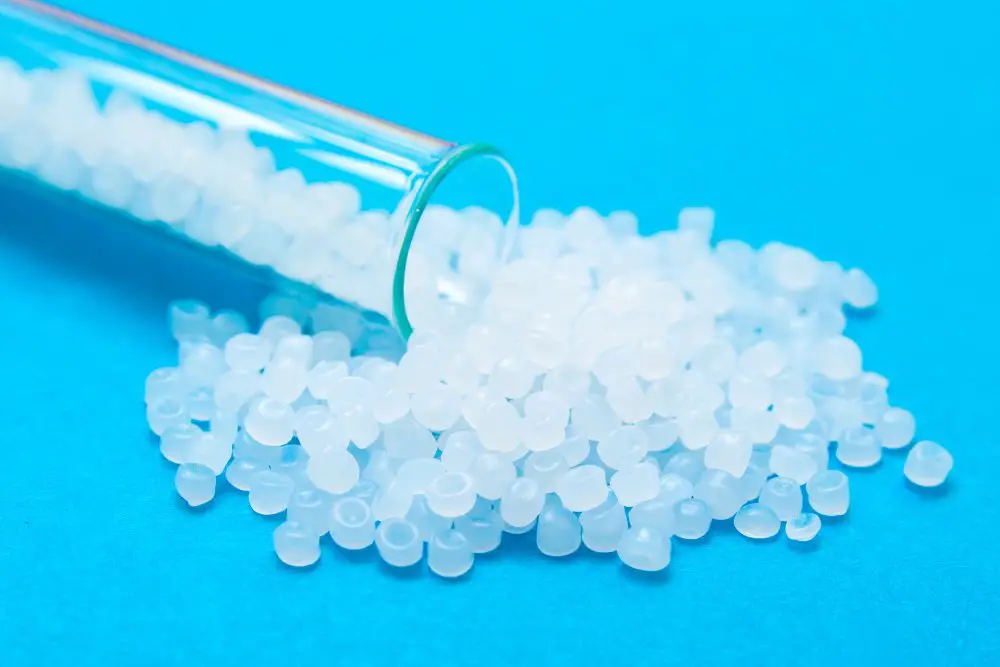
Various types of materials serve their unique purposes in the plastic extrusion process:
- Polyvinyl Chloride (PVC) is commonly used due to its high resistance to oxidation and degradation. It also boasts impressive rigidity and strength, contributing to a highly durable final product. PVC is extensively used in construction materials such as window frames and pipes.
- High-Density Polyethylene (HDPE) provides excellent impact resistance and tensile strength. This material is a popular choice in manufacturing sturdy items like containers and plastic bottles.
- Polypropylene (PP) is known for its high melting point and thus its ability to withstand high temperatures without losing shape. It is commonly used in automotive parts, dishwasher-safe containers and carpeting.
- Low-Density Polyethylene (LDPE) stands out for its flexibility, making it a favorite for applications such as shopping bags and squeeze bottles.
- Polystyrene (PS) provides a glass-like transparency and rigidity. Hence, it is the material of choice for products that require a clear and stiff plastic, such as disposable cutlery, CD cases, and vending cups.
To ensure successful plastic extrusion, it’s essential to select the appropriate type of material based on the intended use of the final product. Different polymers will offer unique qualities, performance, and aesthetics. Ultimately, the choice of material should align with the specific requirements and constraints of the project in question.
Extrusion Equipment: Different Types of Extruders
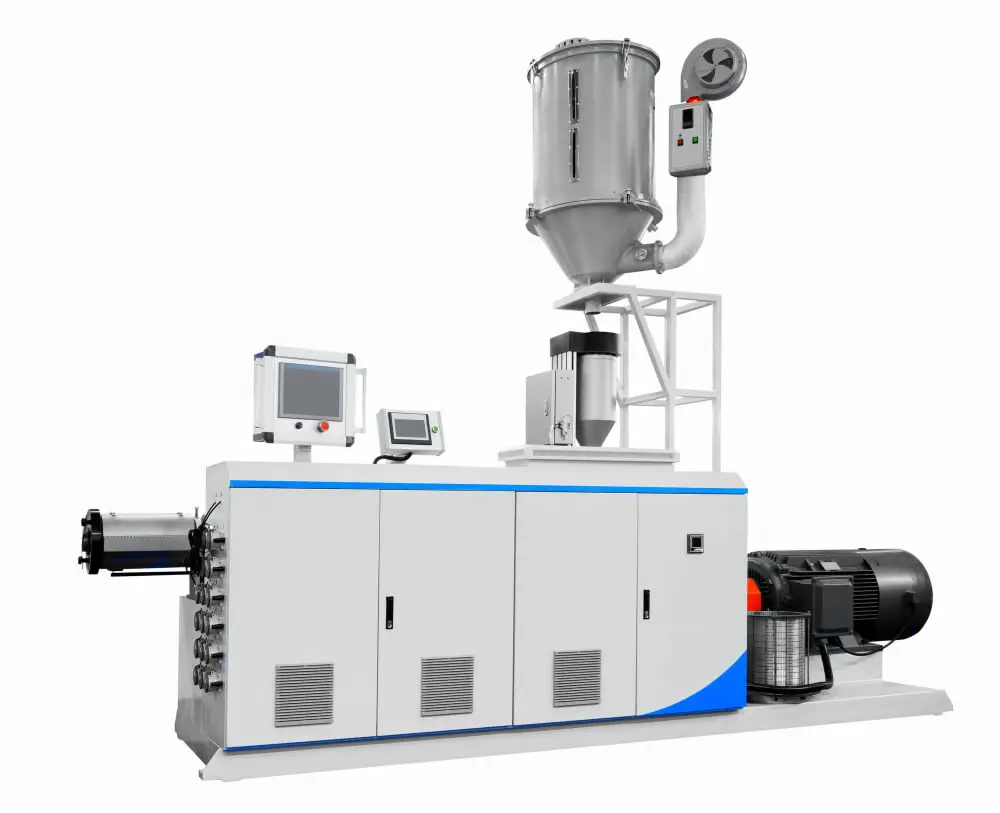
Extruders feature as the core of the extrusion equipment. With an array of variants, let’s explore the commonly used types:
The Single Screw Extruder is one of the most widely used, as it’s robust and versatile, typically applied in creating plastic pipes, fittings, and sheets. The fundamental component is a single heated screw that turns inside a cylindrical barrel, effectively melting and pumping the polymer.
Next in line is the Twin Screw Extruder, designed with two co-rotating or counter-rotating screws within a single barrel. This design is prime for mixing or compounding plastic or polymer materials, offering an elevated level of productivity and mixing efficiency.